Powder Injection Molding (MIM) is a net forming process. In recent years, MIM industry has developed rapidly, and is widely used in 5G Wireless, power tools, locks accessories, medical devices and other industries. The main processes of MIM process include: material mixing, injection, degreasing, sintering, and proper post-treatment if necessary. MIM process has the characteristics of high cost performance, high product performance and forming complex parts.
Tech details
MIM compared with traditional powder metallurgy
✓MIM generally does not require subsequent process
✓MIM parts have excellent corrosion resistance performance, strength and toughness
✓MIM parts have excellent magnetic properties
✓MIM parts have excellent corrosion resistance performance, strength and toughness
✓MIM parts have excellent magnetic properties
Advantages of MIM technology
-
Complex geometry
Because MIM products are formed by a mold similar to the injection mold, a very high degree of freedom in geometric design can be obtained.
-
Excellent material properties
MIM process usually has a production cycle of 5-7 days, and can be continuously supplied after a cycle. The daily output can be satisfied from hundreds of pieces to thousands of pieces according to demand.
-
Suitable for mass production
The high density of MIM products makes them have excellent material properties, which are close to the properties of sheet metal. Therefore, MIM products are especially suitable for the parts with special requirements for product performance.
-
Material diversity
It has been proved that most of materials can be produced by MIM process. But, stainless steel is the best choice.
-
High dimensional accuracy
The dimension accuracy of metal injection molding is generally about +/-0.5%. And, it can reach +/-0.3% under special conditions.
Applications
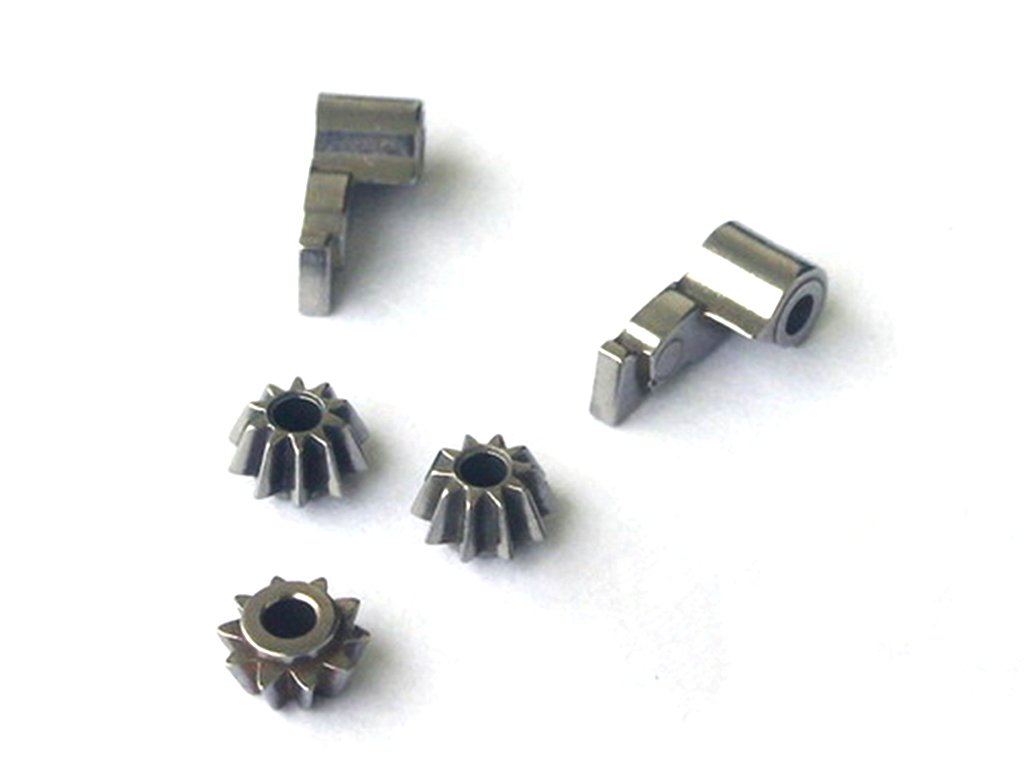
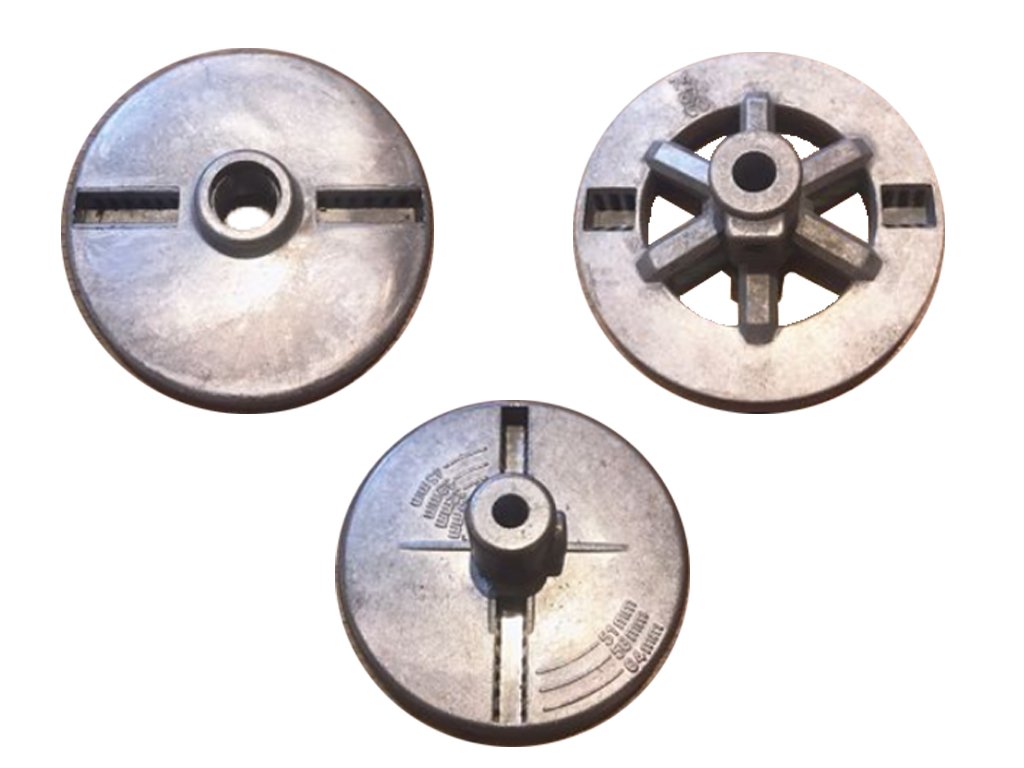
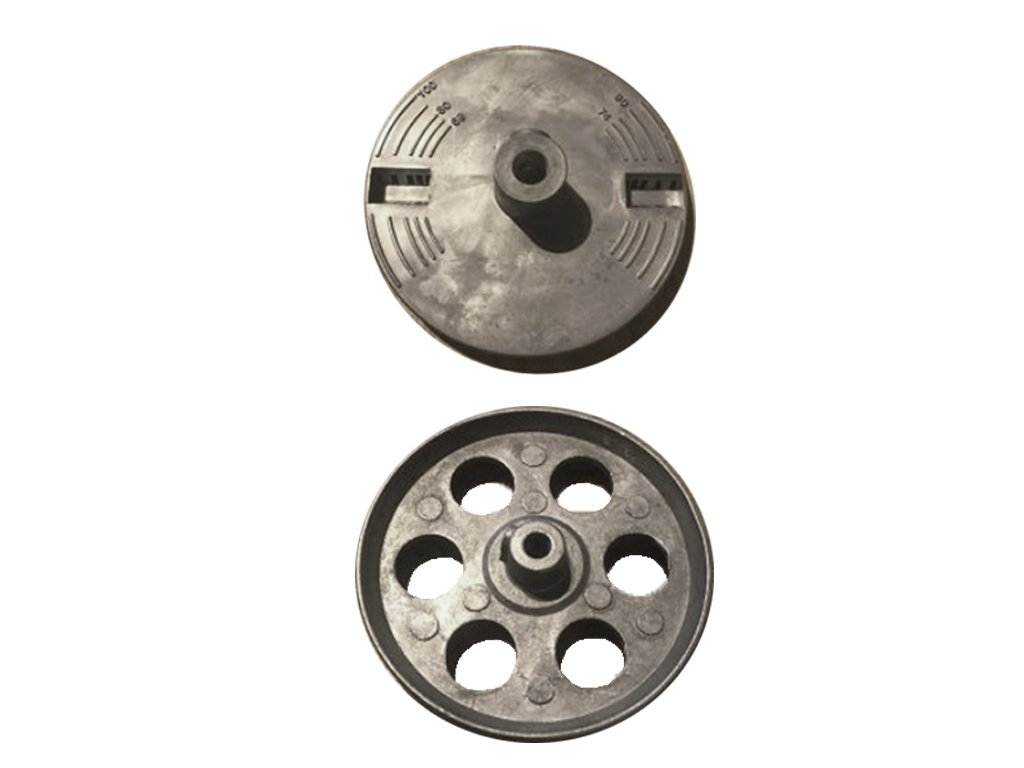
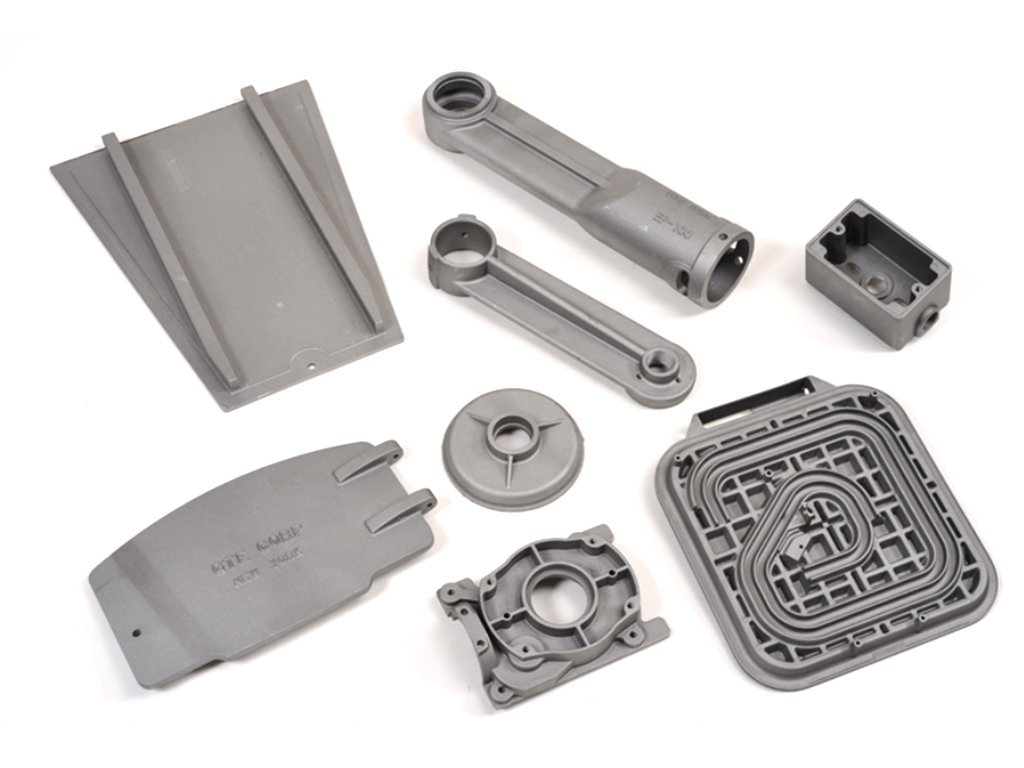