Miniature Diecasting
Miniature die casting is the process to make a very small and complex parts
Special molds design and special diecasting machines are designed specifically for the production of small parts, the process can be used to produce net shape and flash-free parts.
Special molds design and special diecasting machines are designed specifically for the production of small parts, the process can be used to produce net shape and flash-free parts.
Tech details
We are Experts to combine tight GDT and Tolerances below to 0.0005 tolerances and wall thickness of 0.05 in die cast parts that weight up to 0.25 lbs
Some of the important benefits of the miniature die casting process include:
Some of the important benefits of the miniature die casting process include:
✓ Flexibility of part size: The part weight can range from 0.10 to 12.0 ounces.
✓ Possible net shape parts, flash-free.
✓ Miniature die casting process is capable of maintaining tolerance from piece to piece.
✓ The process is fully automated, the manufacturing time and cost is much reduced.
✓ Thin wall die casting: The part weight can be reduced much without the need to sacrifice mechanical properties.
✓ We are here for engineering :The process makes use of engineering
✓ Fast driven of telecom, data, Artificial Intelligence business development, require miniature diecasting chalienges.
✓ Possible net shape parts, flash-free.
✓ Miniature die casting process is capable of maintaining tolerance from piece to piece.
✓ The process is fully automated, the manufacturing time and cost is much reduced.
✓ Thin wall die casting: The part weight can be reduced much without the need to sacrifice mechanical properties.
✓ We are here for engineering :The process makes use of engineering
✓ Fast driven of telecom, data, Artificial Intelligence business development, require miniature diecasting chalienges.
Applications
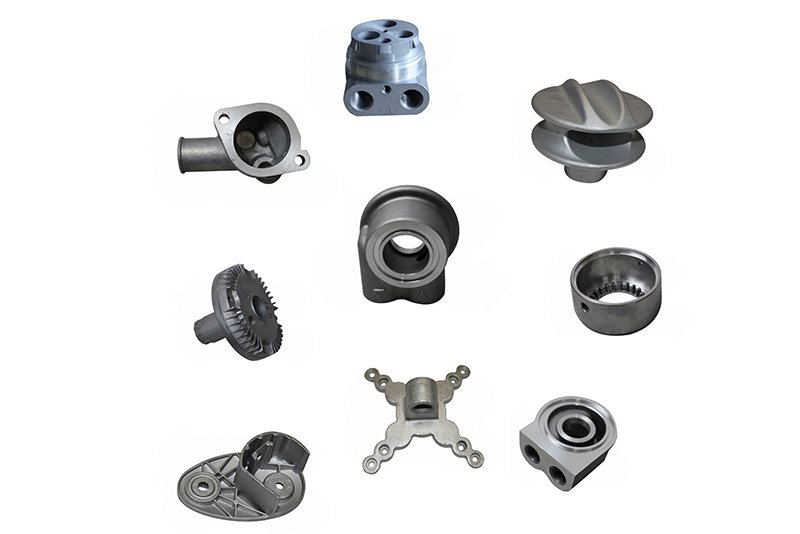
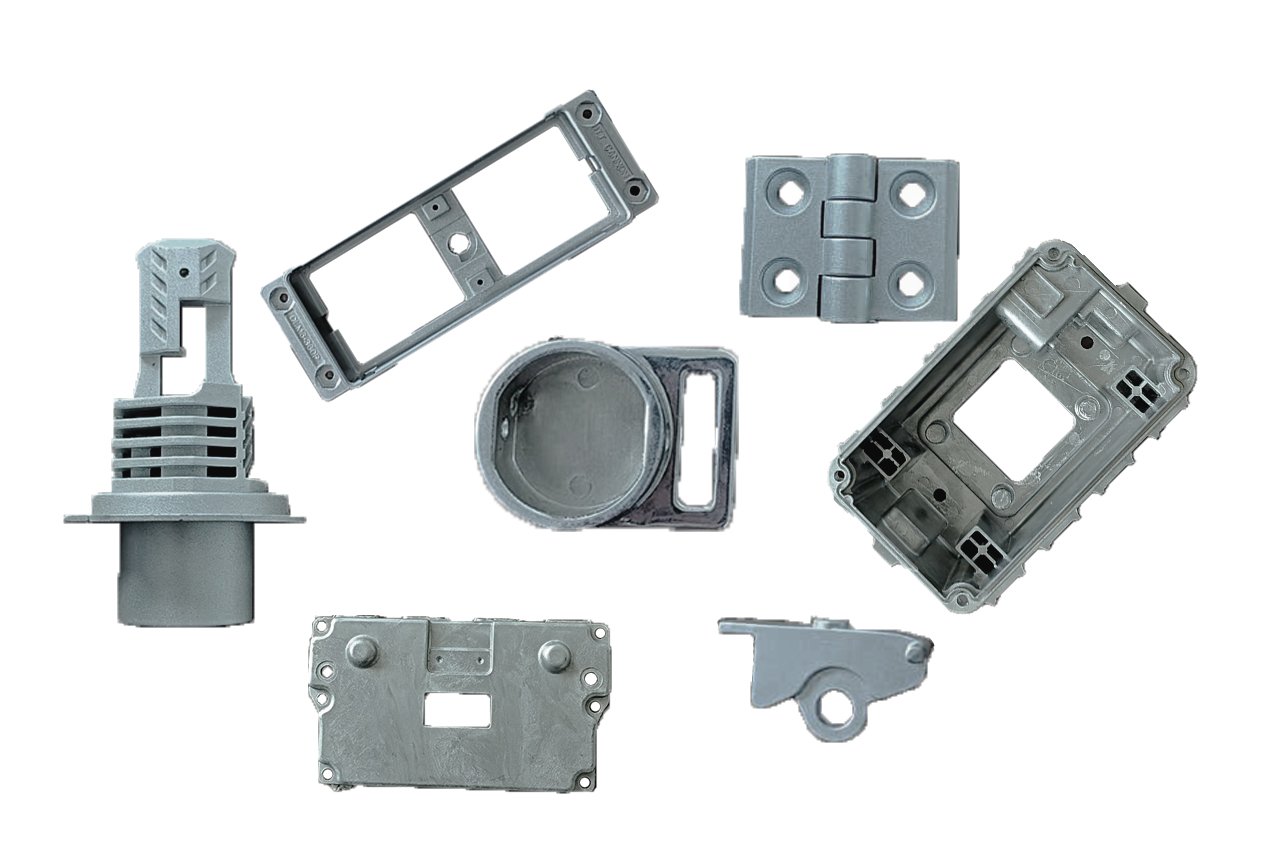
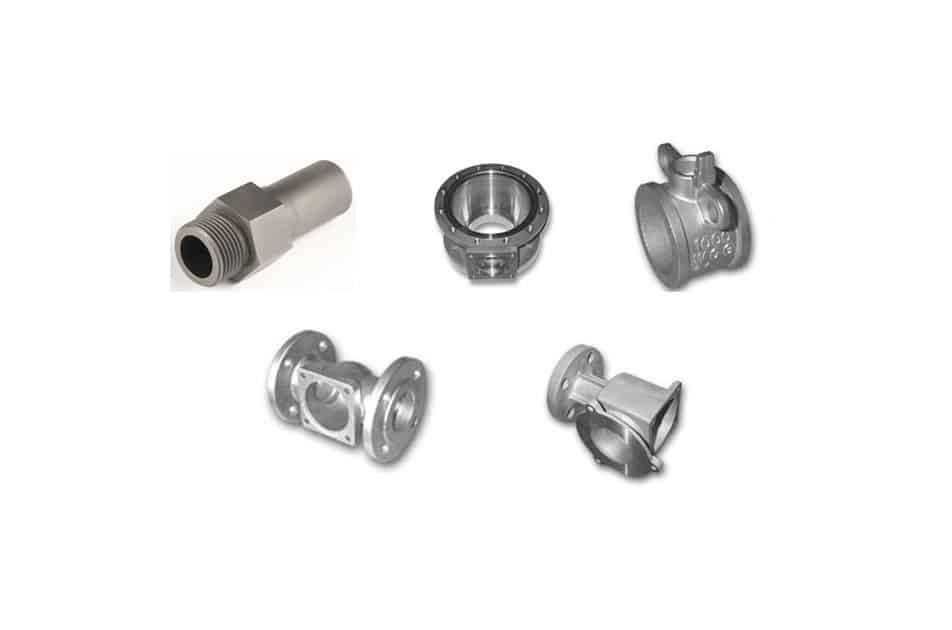
Large Diecasting
Die casting aluminum is a manufacturing method to create metal parts. An aluminum bar should be heated and melted entirely at a high temperature and then forced into the pre-shaped mold cavity to create desired metal parts. The end product comes out with a smooth surface. Most of the time, the finished products don’t need minimal machining and move into the delivery stage quickly. Moreover, the die-cast mold is recycled to manufacture the same parts before it deteriorates. Therefore, aluminum die casting is an ideal manufacturing process for large-scale production. And that is why manufacturers prefer to die casting this and it is popular in various industries.
Tech details
Benefits of Die Casting
✓ EMI, RFI Shielding and can also act as an electrical ground for circuits.
✓ Speed of Production - Die Casting process is highly automated. Multi-cavity dies can also be used to speed up.
✓ Long Tool Life - 100000 - 200000 parts of identical die castings can be produced from a die tooling.
✓ Dimensional Precision - Dimensional tolerance are controlled by mold, thus high repeatability than machining.
✓ Cost Savings - Efficient, economical process for high volume production.
✓ Strength - Produces heat and wear resistant parts.
✓ Good Finish - Die cast parts can be manufactured with smooth or textured surfaces, and are easily plated or powder coated.
✓ Speed of Production - Die Casting process is highly automated. Multi-cavity dies can also be used to speed up.
✓ Long Tool Life - 100000 - 200000 parts of identical die castings can be produced from a die tooling.
✓ Dimensional Precision - Dimensional tolerance are controlled by mold, thus high repeatability than machining.
✓ Cost Savings - Efficient, economical process for high volume production.
✓ Strength - Produces heat and wear resistant parts.
✓ Good Finish - Die cast parts can be manufactured with smooth or textured surfaces, and are easily plated or powder coated.
Material Grades
Aluminium is the most common material for high-pressure die casting, however, we can also cast Magnesium and Zinc. If you require a specific grade not listed here, please do contact us to discuss your requirements.
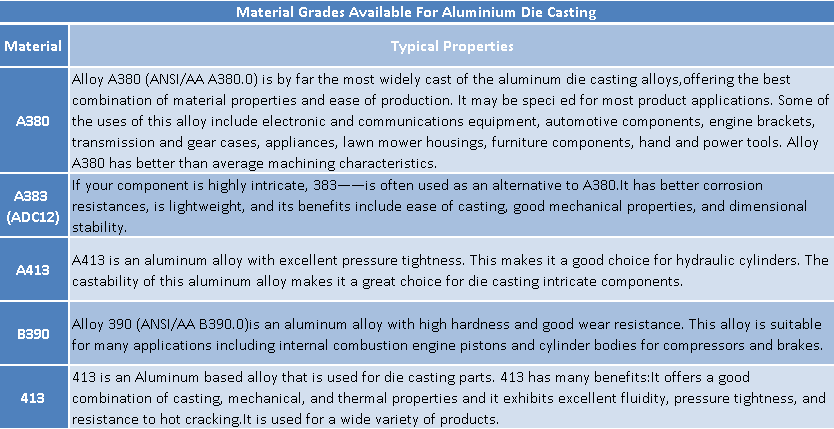
Applications
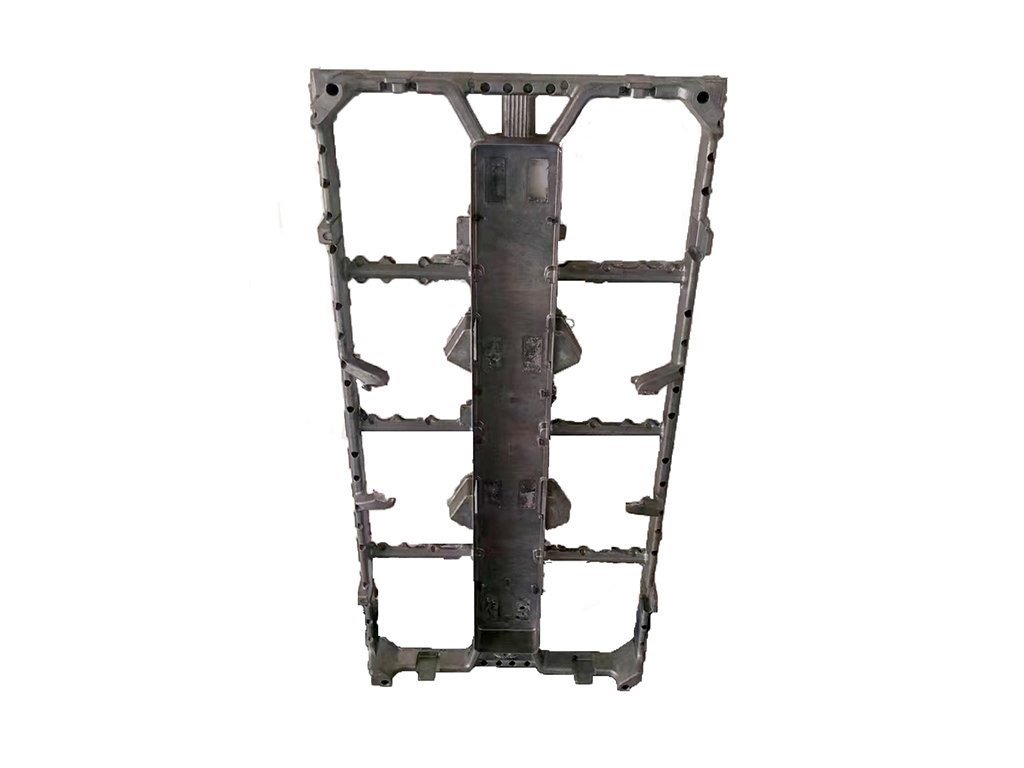
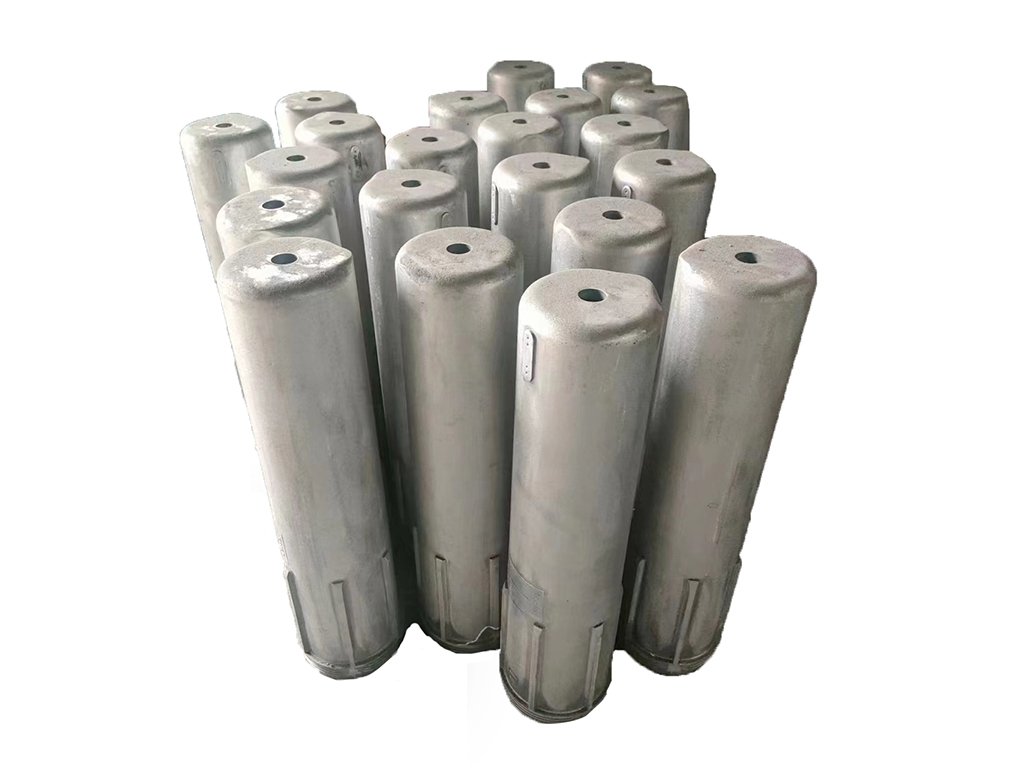
